Trend .NET Production
Trend .NET Enterprise gestisce diverse tipologie di produzione: ETO & MTO,
MTS e ATO. I moduli integrati MRP I, MRP II, MES insieme allo schedulatore permettono un controllo completo di tutto il ciclo produttivo.
Aziende di produzione
La flessibilità, l'ambiente di sviluppo SDK integrato, il numero elevato di moduli disponibili nella piattaforma ERP Trend .NET Enterprise ne permette l'utilizzo nei più svariati settori produttivi.
Trend .NET Enterprise è il gestionale di produzione attualmente utilizzato da aziende nel settore della plastica, del vetro, del legno, della robotica, dell'automazione industriale, coprendo le esigenze di tutti i reparti dell'industria.
PRODUZIONI ETO & MTO – MTS – ATO
MATERIAL REQUIREMENTS PLANNING (MRP I)
VARIANTI E CONFIGURATORE DI PRODOTTO
INTERCONNESSIONE STRUMENTI DI PROGETTAZIONE CAD-CAM
CRUSCOTTO AVANZAMENTO DI PRODUZIONE
MRP II – LA PROGRAMMAZIONE DELLA PRODUZIONE
SCHEDULATORE DI PRODUZIONE A CAPACITA’ FINITA
GESTIONALE DI PRODUZIONE
DIVERSE TIPOLOGIE DI PRODUZIONE: ETO & MTO – MTS – ATO
La flessibilità e la praticità delle procedure dei moduli dell’ Area Produzione sono state accuratamente progettate per rispondere immediatamente alle esigenze dei clienti e del mercato. Questi moduli consentono un controllo semplice ed efficace dei reparti, grazie al quale, gli addetti sono in grado di pianificare correttamente le lavorazioni. Nello stesso tempo possono monitorare gli avanzamenti e sviluppare una visione d’insieme completa, supportando al meglio i processi decisionali dei responsabili preposti a gestire la produzione. Il software gestionale ERP TREND .NET è stato concepito per soddisfare le esigenze di diverse metodologie produttive: produrre su commessa (ETO & MTO), produrre per l’immagazzinaggio (MTS), assemblare sull’ordine (ATO).
Material Requirements Planning (MRPI)
Nel programma gestionale produzione, l’elaborazione MRP I (Material Requirements Planning) avviene sulla base del piano principale di produzione. Secondo la logica produttiva dell’azienda, l’ MRP I esegue una sequenza di elaborazioni prima di elencare i fabbisogni e generare le proposte di approvvigionamento di materie prime, il fabbisogno di produzione dei semilavorati o prodotti finiti e l’elaborazione degli ordini di conto lavoro che dovranno eseguire i terzisti. Le proposte di approvvigionamento vengono effettuate tenendo in considerazione i Lead Time, le scorte minime ed i lotti di produzione.
L’MRP I può essere configurato per essere utilizzato nelle varie metodologie di produzione adottate dall'industria, M.T.O (Make To Order), M.T.S. (Make To Stock), MixedMode (Per le aziende che hanno linee di prodotto realizzate con metodologia M.T.O. ed altre linee di prodotto realizzate con metodologia M.T.S.).
La gestione delle varianti e del configuratore di prodotto, la possibilità di parametrizzare i cicli di lavoro e la gestione della distinta base parametrica permetto un’agevole gestione del flusso ed emissione degli ordinativi di acquisto anche in industrie con un’elevata complessità di prodotto.
AVAILABLE TO PROMISE (A.T.P.)
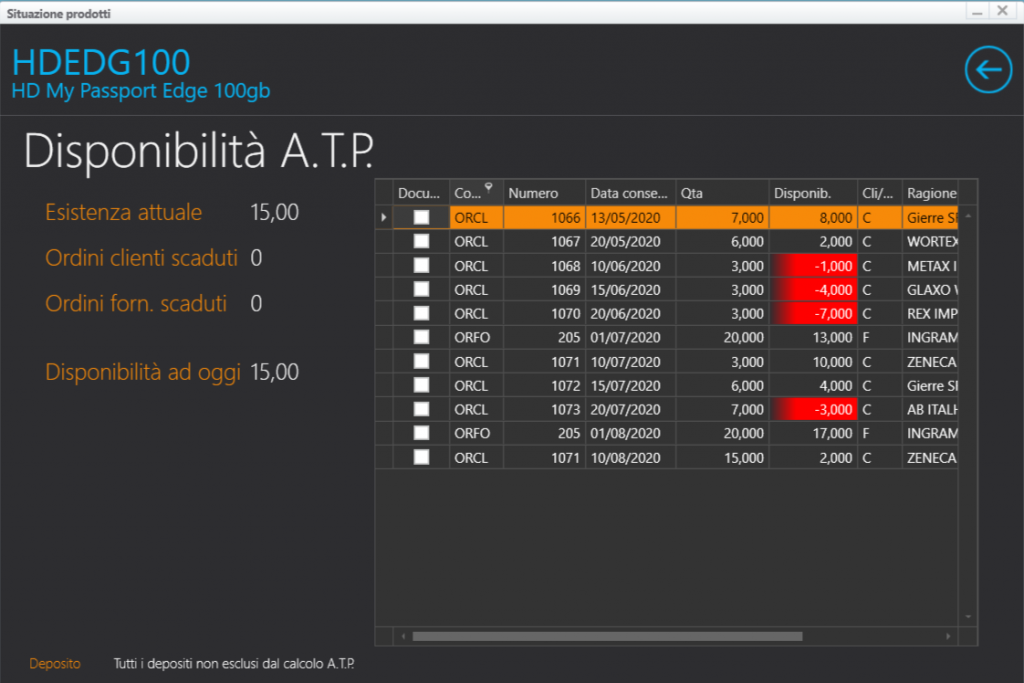
L’ A.T.P. (Available To Promise) è un concetto importante nella gestione della catena di approvvigionamento, che significa quotare una quantità disponibile e una data di consegna per un ordine richiesto da un cliente. L’ A.T.P. integrato nelle metro analisys, ad esempio, permette di identificare immediatamente la mancata disponibilità di un certo articolo ad una certa data e per un determinato lasso di tempo, questo per permettere all’ufficio acquisti di anticipare le date di consegna degli acquisti oppure posticipare le date di consegna ai clienti.
L’ A.T.P. viene calcolato in fase di esecuzione degli M.R.P. predisponendo allert su richiese di anticipo delle date di consegna.
Dall’anagrafica dell’ articolo è possibile attivare la Metro Analisys, uno dei cruscotti disponibili è proprio la disponibilità A.T.P. che evidenzia in rosso le disponibilità negative alla data indicata.
DISTINTE DI BASE
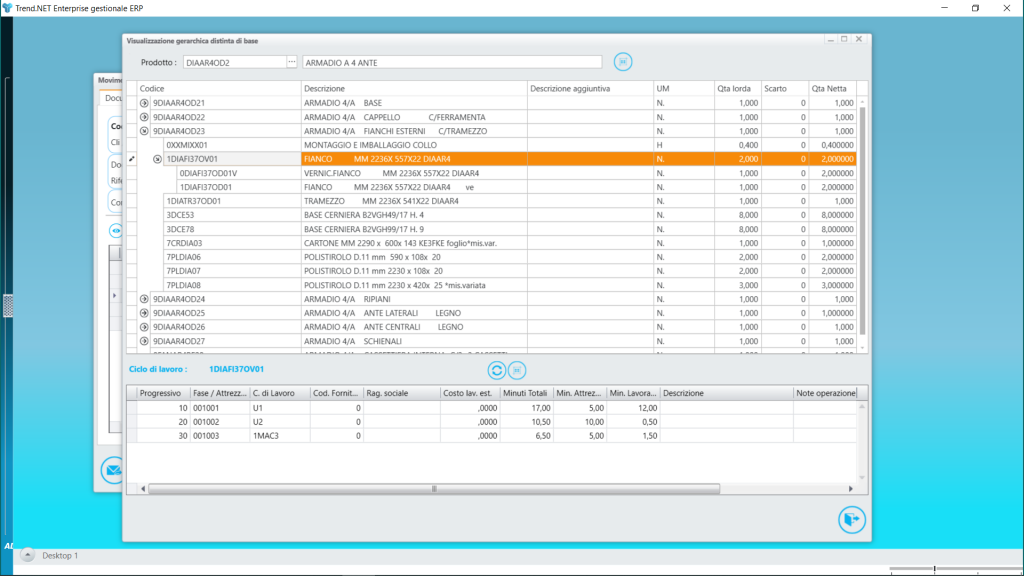
Il modulo distinta base del gestionale produzione Trend .NET Enterprise è completo e molto sofisticato. La distinta base, si divide in due parti: una, relativa ai materiali impiegati per produrre i componenti e il prodotto finito con una gestione ad infiniti livelli, l’altra relativa ai cicli di lavoro necessari per la produzione dei singoli componenti.
La distinta di base elenca, disponendoli su vari livelli, infiniti livelli, i semilavorati che compongono il prodotto finito e che a loro volta contengono i materiali (o semilavorati ulteriori) con i quali sono costruiti. Su questo elenco si basa anche il carico e scarico dei materiali e dei semilavorati durante le fasi di produzione, il modulo MRP I per l’approvvigionamento dei magazzini, l’MRP II per la programmazione della produzione, le procedure per la formulazione del prezzo di vendita.
Una delle funzioni interessanti che il software gestionale ERP dispone è la possibilità che i livelli possano essere configurati per interagire con le varianti impostate nel configuratore di prodotto e, in base alla variante scelta, possono subentrare gli uni rispetto agli altri durante il funzionamento delle procedure suddette. Un esempio potrebbe essere la distinta base di un motore e la variante diesel o benzina: la scelta dell’una rispetto all’ altra consente ai moduli citati di seguire un “ramo” della distinta oppure ciclo di lavoro completamente diverso dall’altro.
VARIANTI E CONFIGURATORE DI PRODOTTO
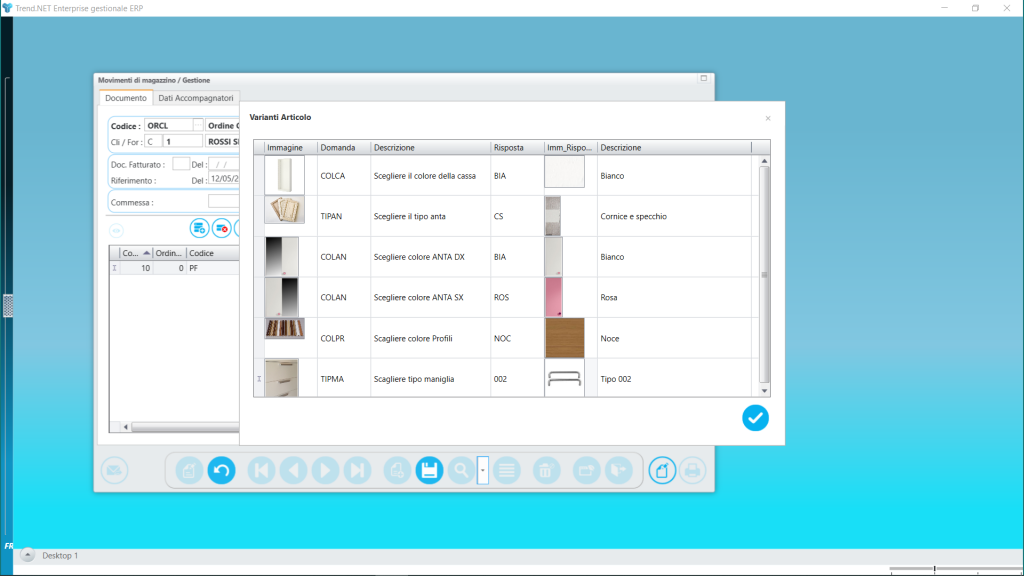
Una delle caratteristiche fondamentali della distinta base di Trend .NET Enterprise è la possibilità di gestire la distinta base neutra. La distinta base neutra e il configuratore di prodotto sono parte integrante del core dell’applicazione ERP, questo significa che è integrata e gestita in tutti i moduli dell’ applicazione.
Nel configuratore di prodotto è possibile indicare una o più caratteristiche dei propri elementi (colore, lavorazione, tipologia di materia prima, tipologia di accessorio, …) l’ elenco delle caratteristiche viene definito dagli operatori in funzione del prodotto che devono produrre o commercializzare.
E’ possibile, infatti, creare una distinta materiali in cui, per questi stessi componenti, le proprietà non sono specificate. Questo significa che non è necessario creare un numero enne di distinte base in funzione delle possibili combinazioni tra le proprietà dei suoi componenti, ma una unica distinta, neutra, associata ad un criterio di configurazione delle sue varianti. Se ipotizziamo, ad esempio, la distinta base di una porta, prodotta in dieci colori diversi con dieci tipologie di maniglie e con apertura a destra e a sinistra, le combinazioni possibili sarebbero un numero troppo elevato per costruire tutte le singole distinte base e tutte le anagrafiche relative dei prodotti contenute in esse; se la stessa porta avesse anche un componente in vetro in 10 varianti di colore le combinazioni salirebbero esponenzialmente. La distinta base neutra, quindi, consente di gestire le combinazioni di varianti senza causare la proliferazione dei codici anagrafici e la relativa impossibilità di gestione. Perciò, in caso di ampliamento delle varianti (aumento del numero dei colori, delle tipologie di maniglia, …), non è necessario creare nuove distinte o nuovi codici articoli, ma solo estendere la lista delle risposte alle varianti. La manutenzione delle distinte e dei relativi codici articoli, gestita in questo modo, è relativamente poco impegnativa, e saranno più pratiche le procedure di ricerca dei codici negli archivi.
Cicli di lavoro
Il ciclo di lavoro riveste un’importanza basilare nella gestione della capacità produttiva dell’azienda. Rappresenta la sequenza delle fasi di lavoro, e quindi dei macchinari o risorse utilizzate, per costruire i componenti presenti in distinta base.
Ogni semilavorato, assemblaggio di semilavorati e prodotto finito, è legato alla sequenza delle lavorazioni necessarie per produrlo, che è chiamata ciclo di lavoro standard. L’elenco delle lavorazioni è caratterizzato dai seguenti dati: il progressivo (è un numero che può essere utilizzato per ri-ordinare la sequenza), il codice della fase di lavorazione, quello del centro di lavoro e il centro di costo al quale è associato; segue l’indicazione della durata della fase di lavoro per unità di prodotto, suddivisa in tempo di “attrezzaggio” e di lavorazione.
Per ogni fase di lavoro, quindi, il ciclo di lavoro standard concorre a “consumare” la capacità produttiva dei centri di lavoro che comprende, quando il prodotto, al quale è associato, entra in un ordine di produzione. Ogni fase di lavoro del ciclo può essere associata ad un fornitore esterno nel caso in cui quella lavorazione venga realizzata da un terzista.
INTERCONNESSIONE STRUMENTI DI PROGETTAZIONE CAD-CAM
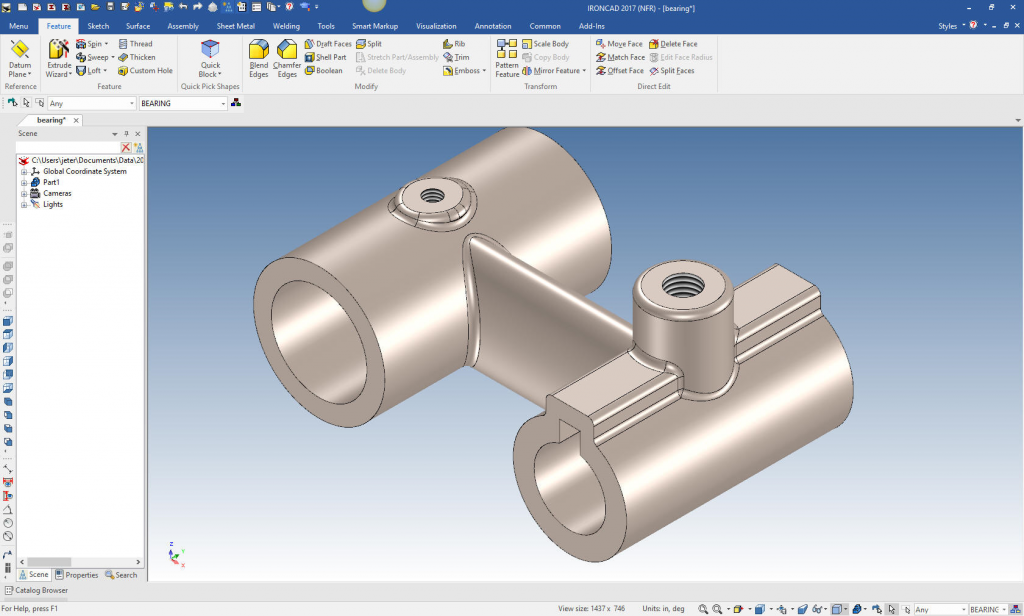
Il modulo di interconnessione a strumenti di progettazione CAD-CAM permette all’ utilizzatore di TREND di creare automaticamente le distinte di base ed i cicli di lavoro direttamente dal progetto CAD-CAM 3D. Nel corso degli anni abbiamo sviluppato diversi driver per i più diffusi software di modellazione solida presenti nel mercato. Anche nel settore dei gestionali di produzione del mobile e arredamento sono stati sviluppati driver per i software di ambientazione maggiormente presenti nel mercato, questo permette, ad esempio, alle aziende produttrici di cucine, camere componibili, camerette per bambini, contract, eccetera di automatizzare completamente il flusso della produzione partendo dalla preventivazione fino alla realizzazione e consegna al cliente.
L’interconnessione con i P.D.M. presenti nell’industria, permette di automatizzare l’integrazione dei progetti C.A.D. con il modulo documentale di TREND .NET associandoli automaticamente ai relativi componenti da produrre, questo semplifica il flusso degli ordinativi ai terzisti oltre che il flusso della produzione interna essendo essi integrati con il M.E.S. di TREND .NET. Sarà quindi possibile aprire il progetto tecnico direttamente a video e mostrarlo agli operatori nei reparti di produzione durante la fase di produzione del particolare stesso.
CRUSCOTTO AVANZAMENTO DI PRODUZIONE
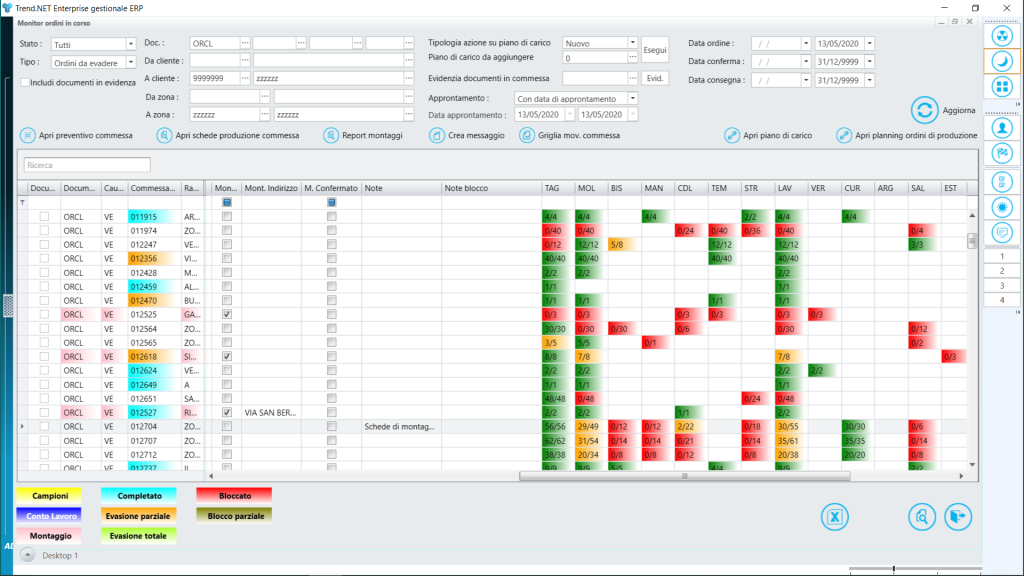
Il cruscotto di produzione permette di ottenere una situazione sintetica della situazione dell’avanzamento in produzione. La tecnologia global di TREND .NET permette poi di consultare il dettaglio desiderato con un semplice click del mouse.
Nel cruscotto vengono visualizzate tutte le commesse in lavorazione con lo stato di avanzamento nei singoli reparti di produzione.
I vari colori delle righe e colonne presenti nel cruscotto permettono di visualizzare e filtrare tutte le commesse in lavorazione in base al proprio stato.
Il cruscotto di produzione è integrato con altri moduli dell’ ERP Trend .NET Enterprise, ad esempio è possibile gestire e creare un piano di carico direttamente dal modulo di produzione selezionando le commesse completate per programmarne la spedizione.
I cruscotti di produzione possono essere modificati con l’SDK di Trend .NET Enterprise per integrarli con funzionalità necessarie all’industria.
GESTIONE DEL CONTO LAVORO
La gestione del conto lavoro, la gestione del conto deposito, la situazione delle esistenze nei depositi dei terzisti, l’ approvvigionamento dei depositi dei terzisti possono essere configurati con estrema semplicità agendo sulla configurazione dei parametri dei documenti di magazzino. In ogni documento di magazzino è possibile definire la logica e la modalità di movimentazione o impegno dei vari depositi. Ogni deposito può essere associato a fornitori, terzisti o clienti, quindi TREND .NET ad ogni movimentazione di magazzino riesce automaticamente ad aggiornare la situazione delle esistenze nei depositi correlati.
MRP II - La programmazione della produzione
Il modulo MRP II di Trend .NET Enterprise fa parte delle procedure per il controllo e la programmazione della produzione.
L'MRP II a seguito dell' esecuzione dell' MRP I provvede alla generazione degli ordini di produzione che saranno programmati nella time line di lavorazione dallo schedulatore di produzione verificando la capacità produttiva disponibile nei centri di lavoro in simbiosi con i vincoli di schedulazione.
L’MRP II di TREND .NET è interconnesso al modulo M.E.S (Manufactoring Execution System) integrato in TREND .NET che permette di rilevare gli avanzamenti di produzione ed i relativi tempi di produzione.
SCHEDULATORE DI PRODUZIONE A CAPACITA’ FINITA
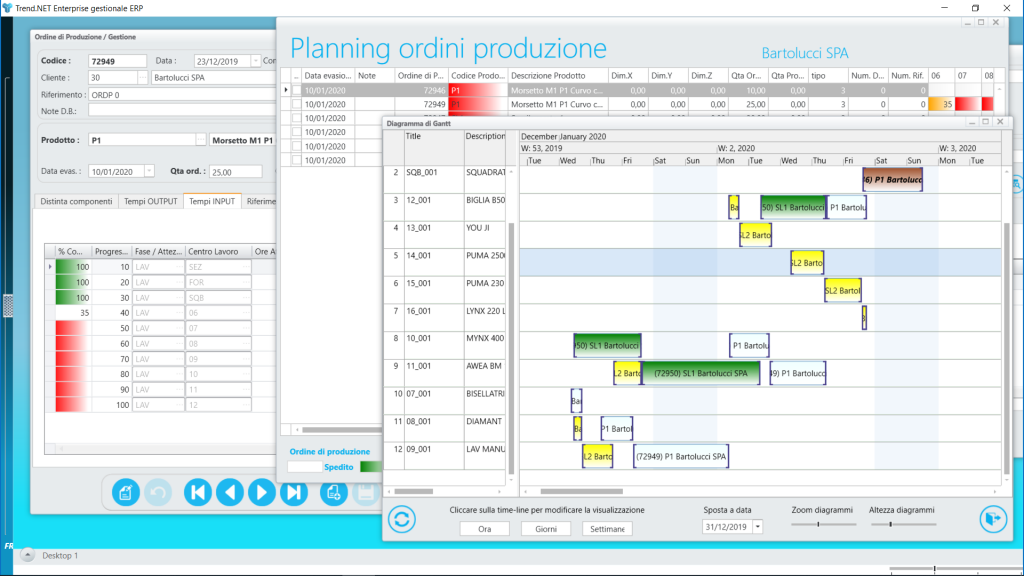
Analizzando le richieste di produzione contenute negli ordini di produzione, le sequenze, i vincoli di produzione, le liste di nesting e le capacità dei reparti produttivi oltre che tutti i parametri di spostamento merce tra reparti, stabilimenti e lead time di ricezione merce dai terzisti, lo schedulatore di produzione ordina e data tutte le singole lavorazioni per cercare di rispettare le data di consegna previste oppure le date pianificate di produzione. Vengono considerate, dagli algoritmi di schedulazione, tutte le gerarchia di distinta di base, tutti i parametri impostati nel configuratore di prodotto e tutti i parametri del ciclo di lavoro per ottenere la realizzazione del prodotto finito e dei relativi semilavorati entro la data richiesta di fine produzione. Gli algoritmi di schedulazione contemplano sia la schedulazione di tipo backwards che di tipo forwards utilizzabile a seconda del modello di produzione desiderato nell’industria. Nel caso in cui lo schedulatore di produzione evidenzia non realizzabili, nei tempi previsti, certi semilavorati e, di conseguenza, i relativi prodotti finiti, questi verranno schedulati nella prima data utile ed evidenziati ai responsabili di produzione che dovranno intraprendere delle azioni per far si che la data di consegna o di produzione richiesta sia rispettata.
La sequenza ottimale di lavorazione viene ricalcolata in base ai dati ricevuti dal M.E.S., tenendo conto dell’avanzamento delle lavorazioni segnalato dagli addetti alla produzione tramite apparecchiature di rilevamento, come i lettori di codice a barre o schermi touch-screen. Eventuali scostamenti rispetto al piano generale di produzione sono segnalati tempestivamente su comodi grafici e report permettendo agli operatori della programmazione una differente pianificazione.
Trend . Net Enterprise un gestionale di produzione in grado di identificare le criticità e proporre nuove soluzioni.
M.E.S. (MANUFACTORING EXECUTION SYSTEM)
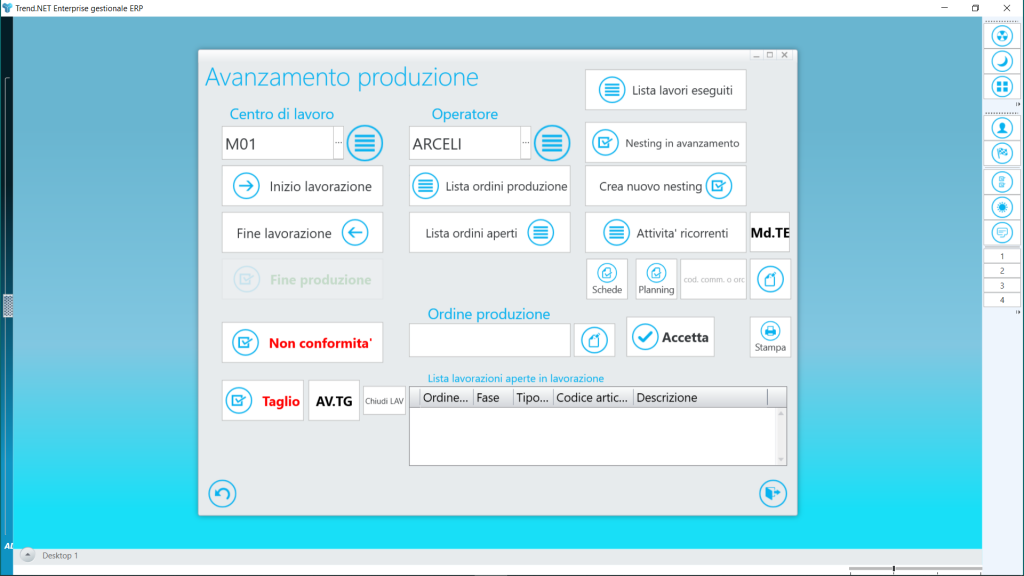
La dichiarazione di avanzamento e la rilevazione dei tempi di produzione rappresentano una delle attività indispensabili per la realizzazione di una corretta schedulazione di produzione. Le metodologie per dichiarare l’avanzamento di produzione sono diverse ma, indubbiamente, le più utilizzate sono effettuate tramite lettori di codice a barre o attraverso l’utilizzo di schermi touch-screen e possono essere utilizzati tutti contemporaneamente, ovvero certi centri di lavoro possono disporre del modulo touch-screen ed altri del modulo bar-code di avanzamento.
INTERCONNESSIONE CON IMPIANTI E MACCHINARI DI PRODUZIONE
Il modulo M.R.P. II dispone di un layer di collegamento a macchinari in produzione completamente programmabile con l’ SDK di Trend .NET Enterprise.
Le interconnessioni possono essere effettuate in modo bilaterale, questo significa che, oltre ad inviare le informazioni necessarie al macchinario Trend .NET riceve le informazioni prodotte dall’impianto stesso e le utilizza per tracciare automaticamente l’avanzamento ed i relativi tempi di produzione.
Le interconnessioni con macchinari o impianti, per essere conformi alla normativa “Industria 4.0” devono essere effettuate in modalità bilaterale.
Unisci alle altre 1000 aziende e industrie, inizia a migliorare i processi produttivi e a ridurre i costi per aumentare i profitti
Non permettere che la tecnologia rallenti la tua azienda, trasformala in asset, contattaci!
Contattaci